Boat builders lagged in adding automation compared to other industries. But today, looking to overcome labor shortages and eliminate potentially dangerous processes, they are eagerly exploring automation of routing and other operations.
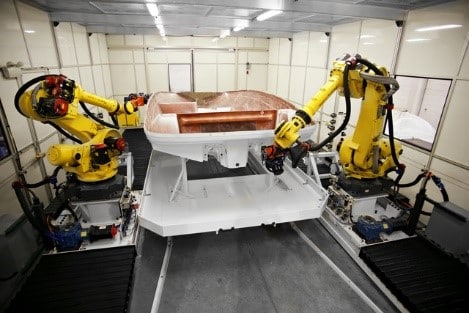
When robotic automation came on the scene, it was quickly embraced by some manufacturing sectors, including automotive and aerospace. Boat builders, for various reasons, were less eager to add robots to the production facilities. That situation has turned around in the last few years. Today, most medium and large boat builders are actively exploring the benefits of automating their processes.
The move toward automated trimming/cutting
Today, almost every boat builder manually trims the edges and internals of open- or close-molded parts using splash guards and manual grinding/routers. It’s an unpleasant dusty job with high turnover. In the past, when job applicants were plentiful, boat builders could readily hire new talent to backfill vacancies or accommodate increased production requirements, although those low-skilled, untrained recruits were likely to have a high rate of production errors.
Today the days of an ample employment pool are gone. Almost every industry struggles to find employees, especially employees willing to perform unpleasant tasks like routing fiberglass. That’s probably the primary driver behind boat builders’ greatly increased interest in looking to automate this and other tasks.
Another impetus for exploring automation, and specifically waterjet cutting, are the inherent dangers of grinding/routing fiberglass. The process creates a lot of dangerous explosive dust (high Kst). Dealing with that dust requires additional ventilation, fire-safety equipment and other costly measures. It also means that operators must wear cumbersome personal protective equipment, including full body suits and hoods, that are uncomfortable to work in and reduce productivity while creating trip hazards and limiting vision.
Automated waterjet cutting is a totally dustless, widely used robotic process that can be a tremendous alternative to routing. One the most common questions automation providers hear from boat builders is, “Will waterjet cutting work in my facility?”
Routers or Waterjets? A Comparison
Trimming parts and cutting openings are the primary applications for robots in boat building. These operations are almost always performed using either waterjet or grinding/router. While boat builders are aware of the basic benefits of waterjet cutting and the drawbacks of routing, it’s not always clear what the right process is for them.
There are some fundamental differences between the processes that will guide boat builders in making the best choice. It’s essential to consult with an automation provider when making these considerations, but there are few factors that point to one method or the other.
Waterjet | Router | |
---|---|---|
Material thickness | Works best with parts no thicker than approximately 1/2″ (0.5″) | Can cut parts up to 3+” thickness |
Material uniformity | Works best with parts with uniform materials | Able to cut parts that include molded-in support materials or other inclusions such as aluminum |
Countersinks, backfires, etc. | Can’t create them | Able to create them |
Load on part | Creates limited to no side load on the part | Creates load on the part that can cause distortion/damage or, if not fixtures properly, thrown parts |
Another consideration is that a waterjet’s effective cutting stream can extend as far as 24 inches beyond the cutting head nozzle. If there are finished materials or structures behind the cut, they can create a problem. There are workarounds to this issue, such as changing the cutting angle or approach. Another is adding protective baffles to deflect or capture the stream, but that could mean additional modification of current layup process, new tools and/or part-trim fixtures.
The cleanliness and precision of waterjets are earning them a place in an increasing number of marine production facilities, but they aren’t the right solution for every application.
Other Automation Opportunities
Boat builders’ primary interest is typically in automating the cutting/trimming process or gel spray, but there are other rich opportunities, specifically in material handling. Using various automated conveyance techniques, parts can be quickly and accurately moved between operations.
Molds can be automatically drawn from storage, delivered to the production line and then returned to storage after the parts have been removed and prepped. And outboard motors can be withdrawn from inventory and delivered to the point of installation using automatic guided vehicles (AGV) rather than forklifts. AGVs can also deliver wiring harnesses and purchased items directly from inventory to the production line for installation. Many repetitive material- or component-moving activities can be automated, speeding production, reducing operator errors and reducing ergonomic risks.
Choosing Automation With Shape
One of the things that held the marine industry back from automating processes was the lack of detail 3D manufacturing models of boat components. Today, those models exist for almost every boat, providing the 3D data that provides the foundation for automation.
In pre-3D days, adding automation meant taking as much as six months to train robots on every boat component for a single model. Having 3D part data shortens that to as little as two weeks, with programming done offline in parallel with the equipment installation, greatly accelerating automation-implementation time.
While automation makes sense in almost every mid- to high-level marine production facility, the factors described above may point boat builders either towards waterjet or router cutting. But there are additional considerations. In fact, it’s common for two marine production facilities that make very similar parts in similar facilities to choose different cutting technologies based on other business considerations. To make the best choice, boat builders need to identify an experienced automation integrator to help guide their decision making and provide the optimum solutions.
Recent Comments